Enamel crafts:
When buying handicrafts, think about the history of that art. Undoubtedly, knowing the history of the value of that art makes it clearer for us. In this article, we describe the history and stages of enamel art.
The art of enameling is one of Iran’s finest handicrafts with a history of 5,000 years. Gold is the only metal that does not oxidize when melted, which is why it is possible to execute a more delicate design on it, but enameling today is mostly done on copper. Mina has been done in different areas in Iran for a long time, but today, in Naqsh Jahan Square, you can see masters who are busy creating this art. In the culture of Dehkhoda, enameling is defined as follows: painting and decorating metals such as gold, silver and copper with special enamel colors that are baked and fixed at a very high temperature.
Enamels
In addition to colorful sights and attractions, each land has other attractive effects and things that we can enjoy. We can immerse ourselves in their bright colors and perhaps receive them as souvenirs. Iran is a very rich country in handicrafts. And the variety of designs and patterns and colors are many. The art of weaving, needlework, embroidery, turquoise work, enameling, etc. has given this land a special glory. Today we want to take you to the beautiful and attractive world of Iran handicrafts to get to know Iranian enameling. Minakari is the Persian word for vitreous enamel. Isfahan is our destination, the modern birthplace of enamel art.
Definition of Mina
Mina means blue sky in Farsi. It is also associated with the word mino which means heaven. This handmade art embodies the azure of the sky itself in its many layers that seem to move towards eternity. This is perhaps one of the reasons why this work of art is called Mina or a representation of the sky. The closest equivalent to this art is enameling, which is also called glass enamel or Chinese enamel. Enameling is applied to several materials such as metal, stone, glass, ceramic and pottery.
Enamel dates back to about 1500 years before Christ. It is an art created with the help of fire, earth and mineral colors. It is elegantly used to decorate all kinds of ornaments and dishes. Dehkhoda’s Persian dictionary defines it as follows:
Painting and decorating metals such as gold, silver and copper with special enamel colors that are baked and fixed at a very high temperature.
The age and history of enameling:
Enamel is the brilliant art of fire and earth, with baked and bright colors, which dates back to 1500 BC and its appearance on metal during the 6th to 4th century BC and after 500 BC. It can be seen. The art of enameling has been manifested in Iran more than in other places, and one of its old examples during the Safavid era was mentioned by the French traveler Chardin, which was a piece of enamel from Isfahan, containing a design of birds and animals on a background of blue flowers and plants. Pale green, yellow and red.
It is difficult to say when the art of enameling became popular in Iran because there are no examples of enameling from the days before the Safavid era (10th century AH) and there are no significant examples left from the Safavid era. However, during the Qajar era, there was a small amount of enameling, and objects such as hookah jugs, hookah jugs, and hookah winders were enameled. There were enameled hookahs in the court of the Qajar kings, especially Naser al-Din Shah, whose hookah playing was one of his hobbies. Also, such enameled objects were available in the houses of nobles and elders of that era. Other objects such as belts, sunbeds, snuff boxes, water bottles, earrings, teardrops and enameled cigarette cans are also available.
The history of enamel art in Iran dates back to the Parthian and Sassanian periods; But its use at the beginning of Islam, before the rule of the Mughal Muslim Ilkhan Ghazan Khan (694 to 703 AH) is not clear. In a short period of time, the king achieved the science of chemistry and unlike his predecessors who spent huge sums of money to find an elixir, he preferred to devote his knowledge and efforts to the art of enameling. The art of enameling can be considered one of the creative inventions of mankind.
The method of making and preparing enamel dishes
First step: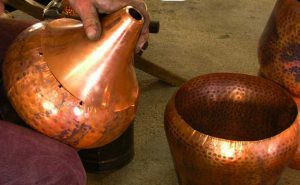
In the construction of Mina, it is the preparation of infrastructure, which is usually prepared in the following two ways
1. Bending method: In this method, a special mold for a plate, vase or any other desired object is placed between the mold and the clamp of the machine. When the sheet is rotated by means of a rod whose head is completely round, they bend the weight on the mold with pressure.
2. Hammering method: in this method, without using a mold and using various types of hammers, hammers, pincers and anvils, objects are prepared in the desired shapes, and after each hammering operation, the piece is placed in the fire and reheated. They hammer it to make it completely in the desired shape
The second step
The collection of various pollutions is from the infrastructure level. The surface of the metal must be completely clean for better adhesion of the enamel glaze.
Third step: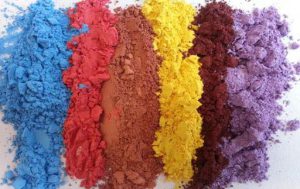
Glaze preparation. Glaze powder cannot be used alone due to its insoluble and high volumetric weight. Therefore, in order to suspend the glaze particles in water and make it more sticky, they use natural thickeners such as “Ba-Dhan”. First, they boil the “grain” until its glaze is obtained, then it is mixed with glaze powder at a ratio of 1 to 10.
Fourth step:
Glazing is done in two ways
- Spray method with a gun: In this method, the glaze is sprayed on the substructure with a gun in a small chamber equipped with strong ventilation, which is called a spray chamber. In this method, some of the glaze is wasted.
- Manual or submerged method: in this method, glaze is poured on the piece to cover its entire surface. This method is preferable from an economic and health point of view in terms of preventing the wasting of the glaze and its particles not being suspended in the air.
After glazing, the glazed objects should be placed in a space away from any dust next to the furnace or in the greenhouse, and must be dusted again by compressed air before placing the object in the furnace.
Fifth step: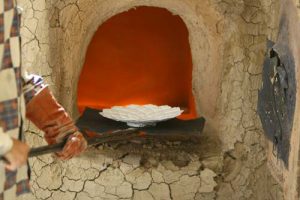
Glaze firing. After the glaze is completely dry and any dust is removed from it, the baking stage begins. To bake the glaze, the temperature of the oven should be around 900 degrees Celsius. The glaze firing process does not last more than 2 to 3 minutes, and when the master craftsman has determined the proper redness of the piece and the glaze and ensured that the glaze is fully baked, the object is taken out of the furnace and placed next to the furnace to cool down gradually. Traditional artisans do not use thermometers; They are only satisfied with experiences and evidence. At this time, the color of the glaze is pea yellow, and with the loss of heat, its color gradually turns white.
The sixth step:
Preparation of paint. The colors used for painting on the enamel background are known as refractory colors and are mainly composed of metal oxide powder. In the olden days, master enamellers prepared these colors themselves, but nowadays ready-made color powders are used. In order to prepare these colors for painting on enamel objects, it is necessary to first mix a solution of gum arabic in water with glycerin in a ratio of 1 to 2 and After placing the desired color powder on the glass and dropping a few drops of the above mixture with a spatula, the color is prepared and used like watercolor colors. In fact, the solution mixture of gum arabic and glycerin acts as a paint solvent (dot). If the remaining paint dries, it is prepared again for painting by adding a few drops of the mixture of gum arabic and glycerin. Color powder can be mixed with pine ink or lavender ink and ready to paint. In this case, it should be done using paint and oil.
Seventh step:
The transfer of the design is on the glaze. For this purpose, first, the enamel artist puts his desired design, which is usually derived from Slimi and Khatai motifs, flowers and chickens, hunting grounds, and face making, on paper, and then the paper is “needle-worked” or “sanded” in such a way that the lines of the design They drill holes close to each other. Then, with ash or soot, they implement the design on the glazed piece.
Eighth step:
It is a painting that can be started by sketching and first sketching the main lines of the design and then coloring different parts. Also, you can paint the design first and then draw around it.
It is important to mention that there is no white color in enamel paints, and if it is necessary to use this color, the artist skillfully uses the white of the background glaze or after painting with a pointed pen, he removes the color from the background until the white color of the glaze appears. to be If there is a golden color in the desired design, at this stage, the painting should be completed with gold water (dot). Also, in the painting stage, if oils such as glycerin or lavender or similar oils are used to prepare the color, it should be done. Before placing the object in the furnace, remove the oil by placing it on an electric stove or a gentle flame (alcohol lamp) or by bringing the piece close to the furnace, because otherwise it is possible that in The surface of the enamel will have pores due to the boiling of these oils and the surface of the enamel will become pockmarked. When painting on enamel, too much color causes fogging and damage to the work during the heating stage. If the color is too much at one point, it should be removed before baking.
Ninth step:
Baking is painting. After the painting on the glaze is finished, the piece must be reheated in the furnace. This time, the furnace temperature should be between 600 and 750 degrees Celsius. If gold is used for coloring, the baking process must be done at a maximum temperature of 450 degrees Celsius, because at a higher temperature, the gold will be destroyed.
It should be noted that enamel heating should be done carefully, especially during the painting firing stage; If the temperature of the furnace or its time is more than necessary, it will cause the color to flow or penetrate into the primary glaze of the enamel. Also, if the temperature and time are less than the limit, the color will not be baked well and after baking it will be well removed from the glaze or become cloudy. After finishing the baking of the enamel painting, it is covered with a thin transparent glaze and baked again.
Finishing work: The glaze does not completely cover the edge of the opening and the base of enamel objects such as vases, plates and various dishes and gives it an unpleasant appearance. To fix this defect, brass or silver strings should be used; In this way, first the brass or silver wire is made into a strip with a width of 2 mm using a rolling machine, then it is passed through a cone-shaped hole to form a gutter. Then, with it, he covered the edge of enamel objects and welded it with silver solder.
Enamel products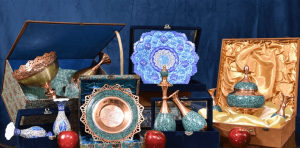
Enamel makers produce different works, some of the most common of which are: *plates, vases, bowls and mugs, photo frames, enamel panels that are combined with other arts such as gilding, inlaying, miniatures and jewelry making.
* Enameled doors, windows and shrines in religious places and for the tombs of Shiite imams in Karbala, Najaf, Samarra, Mashhad, Qom, Hazrat Abdul Azim and other blessed places.
Women’s make-up boxes, inlay and enameling boxes, tea and drinking service, hookah, Koran box, armor, mirror, pencil case, belt, enameling bubbles, water sprayer, photo album, snuff box and dagger sheath.
Earrings, brooches, necklaces, rings and medals.
Another popular handicraft in Iran is pesrian kilim bags, which are produced in different cities.
Enamel making tools
The tools needed to make enamelware are:
- Sheet (gold, silver, copper, Warsaw, iron and brass) was used more than pure gold for its malleability and not oxidizing at the enamel melting temperature.
- mortar
- Aqueous substance of enamel
- copy paper
- Hammer
- Anvil*clamp
- Bow saw and hacksaw
- metal scissors
- Mo pen
- Color (vegetable, mineral or metallic)
- Furnace
- Silica, carbonate, sodium, potassium, lime, tin and lead are also required chemicals.
Types of glaze in enameling
When the copper base of the enamel product is ready, it should be covered with glaze so that the enamel container is ready for design and painting by the master enameller. Enamel glaze on metal is divided into two main categories, which are:
Industrial metallic enamel glaze (matte and transparent)
Art enamel glaze (matte and transparent)
Industrial metallic enamel glaze has more practical aspect and less artistic aspect, but the percentage of its combination with artistic enamel glaze is very high. This glaze can be used on various metals, but iron and cast iron are the main metals on which this glaze is used.
In terms of chemical structure, artistic enamel glaze is considered to be the most suitable according to the type of metal used, compounds and expansion coefficient that is homogenous with the metal, considering all these factors of copper metal. In this method, all kinds of thermal fluxes are used instead of lining glaze. In order to create a good connection between the surface and body glaze, the lining glaze is repeated 2 to 3 times on the body. Like other glazes, art glaze is used in matte, transparent and sometimes semi-transparent form.
Types of enameling
- House-building enamel: in this method, various objects are decorated with thin brass wires in the form of houses.
- Painted enamel in this sub-branch is designed and painted after applying white glaze on the dishes.
- Inlaid enamel is the most difficult field of enameling, in which dishes are decorated with gems or decorative stones.
- Sabi enamel: In Sabi enamel, enameling is done on gold and therefore it is one of the ornaments.
- Lattice enamel: It is called enameling to create different holes with special designs on the dishes.
- Sugar enamel: In this type of enamel, the copper skeleton is covered with colored glaze. This type of glaze has existed before. But today, they cover the copper with white glaze, just like the steps mentioned in the painting enamel, then they paint the entire surface of the glaze with the desired color and heat it in the furnace. Then they design the prepared colored object with a white pencil and the materials that will be mentioned perform the next operation.
Art schools and enamel artists
In the past, there were many renowned masters and artists in Mina, which of course is obvious from the age of Mina’s art, but what is important is that the names of these precious artists have been lost among the pages of history and the events of the time, and only the names of masters like Master Mirza It is not known in what period Abdullah Mosvar Taheri lived.
Master Mohammad Ibn Abd al-Wahid Herati (6th century) is in possession of the works obtained from these artists. Of course, there are many other works whose creators’ names are not known. In the present era, there are great masters who protect the art of the artists of the past and present it to the future, among them are the late master Zarkoni, the late master Sanizadeh, the late master Faiz Allahi, Mr. Ghafarian, Honrdoost, Ismaili, Faqihi. And. . . Cited.