In this article, we want to discuss the art of glass handicrafts because glass is an important part of our daily life. From our childhood memories and the stained glass windows of our grandmother’s house to the types of vases and glass containers that we use today.
After the stone age, man passed into the ancient era. All important civilizations entered the ancient era from the middle of the second millennium BC. The ancient era ended in 426.
In ancient times, people on the eastern side of the Mediterranean Sea, Egypt, Syria, and Mesopotamia traded in natural glass stone and used natural glass stone to make all kinds of beads and pointed beads for hunting and defense.
During this period, the inhabitants of Mesopotamia and its surrounding civilizations used to melt glass. At first, the quality of the glasses was very low and full of unmelted grains and had a dull color. But over time, the quality of glass increased and the quality of glass improved, and the production of artificial glass and beads became popular during the early ancient civilizations. By examining the history of glassmaking in the world, it is possible to understand the origin and expansion of the art of glassmaking in Iran.
Glass art video
Early glasses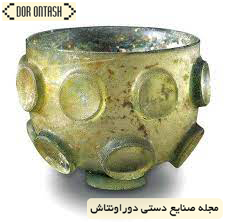
The history of using natural glass is mostly related to making decorative beads and beads and sharp pieces for wooden spears. The oldest glass found in the form of a decorative bead, located in the Euphrates River Delta, dates back to the third millennium BC. Is. The oldest made glasses were found in Western Asia and belong to Alalakh, Nuzi, Ashur and Tell El Rima, which date back to the second millennium BC. glass handicrafts
The Phoenicians, who were merchants of ancient times and traded by sea, were the main traders of natural glass stone at that time, who transported natural glass stone to different places by ships and boats, mostly from areas like Sicily or Carthage.
Changes in glassmaking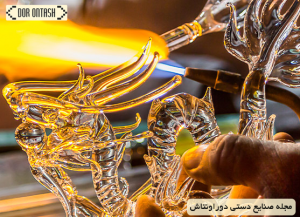
The major developments that have happened in this period in relation to the glass industry can be summarized as follows:
The manufacture of synthetic glass by melting its raw materials is around 2500 years BC.
Mesopotamian glassmakers in 1500 B.C. They succeeded in making glass containers using sand molds.
At the beginning of the first century AD, the greatest revolution in glassmaking was carried out by the Syrians in the city of Sidon, and that method is blown or blown.
The invention of the tail pipe in 50 BC caused the evolution of glass making and making glass production cheaper and increasing production and overall cost control. This invention took place in ancient Rome and spread further in the Eastern and Levant Mediterranean regions.
The main poles of glass handicrafts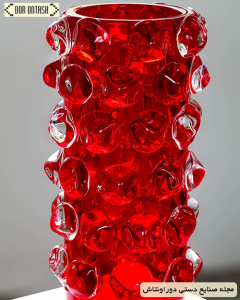
The main poles of glass making in this period were Venice (Italy), Alexandria (Egypt) and Damascus in Syria. But other old poles of this industry, namely Mesopotamia, were more or less active in Iran.
The conscious use of metal oxides and especially the invention of opal and Roman glasses are among the important achievements of the glass makers of this era in connection with the composition and materials of glass.
glass handicrafts in ancient Iran and its evolution until today
The history of glass was also formed in Greece. With the emergence of two new civilizations, Greece and Iran, glassmaking was transferred from Nineveh to Iran and from Egypt to Greece, and in the eastern age, Iranian glass appeared in the process of historical developments of the glass industry, different from the previous trends.
The Iranian glassmaking industry expanded during this time and started a new campaign in glassmaking in the East. The Aryan tribes of Khuzestan and Ilam region, who were the neighbors of Mesopotamia, were familiar with glass and used it since a long time ago, in the second millennium BC, especially during the time of the Elam Empire, whose center was Susa.
With the fall of the city of Nineveh, which was the largest glass-making city in Mesopotamia, the glass-making industry was transferred from Nineveh to Iran.
Chughazanbil
In the hills of the historical ruins of Chaghazanbil and also in the religious temples of this area, the ziggurat, which was built between 1245 and 1265 BC, a large number of dark blue cylindrical glass beads were found with the signatures of Kassite and Elamite glassmakers on them.
A number of beads and beads have been found in Vati Castle in Dilman area, which were made of Iranian white beads in the 1st to 3rd century AD.
In the Sassanid era, there were colorful and cut beads and twin beads, and in addition to beads, all kinds of pendants for ears, necks, clothes and different human and animal shapes were made.
Around the years 1200 to 1100 BC, archaeologists dug and found a number of glass containers, but these glass containers bear the signature of Syrian glass, and it is not possible to determine with certainty the start time of making glass containers. It is not possible to estimate the beginning of the history of glass in Iran with certainty .
In the Marlik region, two glass mosaic vessels were found, which date back to 1200 to 1000 years BC.
In the ruins of Persepolis, glass containers were found, including drinking bowls, bowls, plates, wine cups, and a bunch of broken containers.
Some Aryan tribes, such as the Marlik tribe, who settled on the northern slopes of Mount Alborzo, on the banks of the White River or the southern shores of the Caspian Sea, had access to natural resources, access to gold, silver, and copper mines led to their growth in culture, arts and crafts. and they enjoyed great wealth. And they were placed at a high level of industry and art.
Iranian glassmaking has a kind of independent identity and has had a deep impact on history in decorative and artistic works. The bergamot design that was present in Marlik metal vessels was also present in Iranian glass vessels.
glass handicrafts during the Achaemenid period
During the Achaemenid era, the glass industry was not in a clear state, and the location of the production of these vessels cannot be determined.
One of the most important problems in the history of the glass industry in Iran is that old glass objects have either been stolen or have been taken out of the country by various thieves and antique thieves, and it is not possible to determine the historical sequence of this industry.
Due to its geographical and commercial location, Iran has been a bridge of communication in the ancient world. The arrival of Syrian, Egyptian and Mesopotamian glass in Iran causes the mutual effects of the two cultures. 95% of Iranian glass is in foreign museums.
The ancient empire of Iran collapsed with Alexander’s attack, but after the end of the Hellenic period and the fall of Seleucia to the Parthians, we are faced with the geographical expansion of the glass industry, especially since with the creation of the Silk Road, Iran became the meeting point of East and West and on the trade route of the Roman Empire. And China was placed.
Archaeological excavations show that the production of glass objects and containers in the north, northeast, west, and especially the old areas of the Tigris and Euphrates reaches a high level in terms of quantity and quality, and Iranian glass has a relatively good market in China, Japan and most of the Far East countries. obtains Of course, in terms of shape and working methods, Iranian glass has a lot of harmony and similarity with Roman glass, and this is a sign that there was cultural mixing on the one hand and commercial competition on the other hand, between these two empires.
During the Sassanid era, glass cutting reached its peak and Iranian polished dishes were exported to the east and west. In the great museums of the world, many examples of this carved container are kept and they are considered as exclusive examples of Iranian glass in the ancient era.
Iranian glassmakers used special decorative methods to make glass. For this reason, the demand for Iranian glass was high in the East and West, and at that time it was more accepted in the world.
glass handicrafts after the emergence of Islam
The most important social development of the 7th century AD was the emergence of Islam and its special culture, which by dominating the world, especially Alexandria, Damascus and Mesopotamia, glassmaking entered a new stage of development, and in the history of eastern glassmaking, this period is known as the glass of the Islamic era. .
Glassmaking in the Islamic era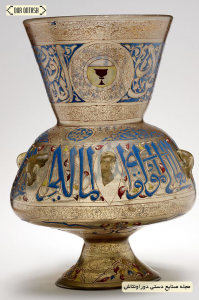
One of the most important styles in the history of glassmaking in Iran and the world is the Islamic style. We know that the 3rd and 4th centuries of Hijri are considered the golden periods of Islamic civilization and we can even see this progress in arts such as glass making. Some of the innovations of Islamic glassmakers are:
1. The invention of the “wheeled glass” method in the 7th century AD to produce flat glass
2. Inventing deep cutting methods on glass to create beautiful images
3. Making glass jars, containers with lids, lighting bulbs and base containers
4. Combining the art of glass making and enameling for plating glass containers
2500 BC | Glass mold for works such as gemstone beads | Mediterranean |
1550 BC | Core shaped containers | Mediterranean |
1380 BC | Built-in core-shaped containers | Egypt |
799 to 700 BC | Mosaics, lost wax moldings | Phenicia |
100 BC | The Roman Empire and the development of blown glass | The Roman Empire |
14 AD | Collapsed and melted mosaic vessels | Mediterranean |
15 AD | Mass cutting and turning, deformation of blocks | Egypt |
The above picture is related to the glass container of the 3rd and 4th century AH. The place where this ancient Iranian container was discovered and where it is kept is the Los Angeles Art Museum.
glass handicrafts achievements of the Islamic era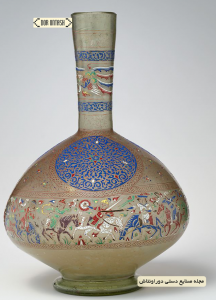
The following are considered the most important achievements of glassmaking in the Islamic era:
- The invention of the wheeled glass method to produce flat glass was made by the Syrians around the 7th century AD.
- Deep carving , which is the basis of painting on glass.
- Glass tights with a long and narrow neck.
- Making containers with lids and bases .
- Evolution in the form and method of enameling and the use of glossy glaze and plating and making enameled glass, the emergence of new applications.
- Glass for making light bulbs for chandeliers and bottles .
Glass making in the middle of the 16th century: Popularity in Europe and innovations in Venice
From the middle of the 16th century onwards, due to the changes and asceticism of the West, the stagnation of glassmaking in the East began, and Europe became the major producer of glass, and the Venetians became the pioneers of changes and innovations in the glass industry . Even the shapes and decorations express rebellion and celibacy in Europe.
Developments of glass handicrafts in the late 19th century: the use of machines to produce glass
Glass making in Europe expanded geographically and became popular in Spain, Germany, Czech Republic, Slovakia and England. All kinds of lead and brosilicate glasses were invented and in the last stage of the geographical expansion of this industry, it was transferred from Europe to America, and finally, at the end of the 19th century, the use of machines to produce glass entered this industry, and fundamental developments in furnaces and machines in the process Glass was produced.
Glassmaking in the 20th century: fully automatic glass production lines
In the 20th century, we see the construction of fully automatic glass production lines, glass machines entered the market in the form of electrical-mechanical wonders at a high speed.
The furnaces for the production of glass containers with the melting power of one hundred thousand tons per year are the glorious manifestation of the dream of the ancient glass makers who burned their human thoughts for centuries in their small workshop furnaces to make a simple glass container.
The history of glass handicrafts in Iran
The history of glass containers in Iran goes back to the formation of the first civilizations. In the table below, you can observe the types of glass and glassmaking in Iran by historical period: iran handicrafts
Historical period | Characteristics of the style of glazing |
pre-historic | The presence of glass bottles in the discoveries of Marlik and Chaghaznibel civilizations |
Achaemenians | The types of glass beads that have been seen in black and white colors and are now on display in Tehran’s Abgineh Museum. |
The Sassanians | The lapis lazuli and cut glasses of this period were very famous in China and were called Sasanian glass. |
Parthians | Production of glass cups with reliefs |
The Seljuks | The pinnacle of hand-made glass industry in Iran – making glasses with a very small diameter (in millimeters) |
The Mongols | The loss of glass making and the advancement of tiling and pottery |
Safavian | The revival of the production and use of glass, especially by Shah Abbas |
The Qajarians | The introduction of industrial methods of glass making and the import of foreign glasses – the decline of manual glass making |
As we can see, with the modernization of the world, manual glassmaking gradually declined. However, we still see the existence and activity of these workshops in some cities of Iran and the world (such as Tehran, Isfahan, Shiraz and Venice in Italy).
Materials used in glass handicrafts
Different materials and combinations are involved in the manual method of making all kinds of glass. However, the basis of the formation of any kind of glass is the presence of a substance called silica and its derivatives. Melting elements such as sulfate, carbonate and sodium acetate are used to liquefy and lubricate flint or porcelain stones so that the melting point of silica is lowered and it becomes fluid.
Materials such as calcium carbonate help to mix silica and sodium compounds well during the melting stage.
Glass tools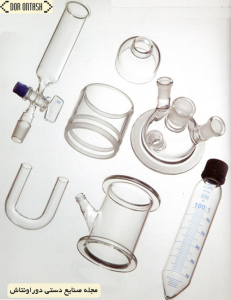
- tail rod
- Stoner
- wooden spoon
- Water machine
- Board template
- scissor
- blade
- And…
Glass crafts
Perhaps we can consider the same initial container that comes out of the glass workshop as a kind of handicraft. But the artists with the taste of our country have always tried to produce many times more beautiful objects by combining all kinds of arts with each other. In the following, we will introduce some of these arts in which glass is used:
painting on glass
Stained glass is one of the most popular handicrafts in the world. In this art, beautiful patterns are drawn on the glass using special tools and colors, and then their color and design are fixed by placing them in the furnace. The use of this type of glass in architecture and interior decoration is very evident.
Miniature glazier
Another very beautiful art that emphasizes more on making glass than on its finishing is the art of miniature glass making. The objects created in this field are all familiar to us, but they have very small and miniature dimensions and are used as a decorative device.
Hand print on glass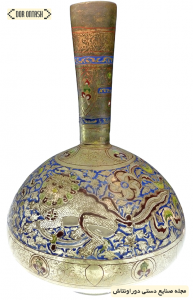
Monoprint or printing on glass is a method of manual illustration in which the artist prints his design beautifully on the paper using the smooth and polished surface of the glass.
Glass making training
Glass tools and materials
Among the tools and materials used in glass making, the following can be mentioned:
Silica stone (which is used to save glass shards),
colored materials for coloring glass, such as cobalt oxide, copper, iron, manganese, sulfur. The colors used are in the form of powder and can be mixed with a special solvent, and soluble colors are prepared from metal oxides.
Special stone and milling tools are used for carving on the glass, and the designs and lines created by using the stone are deeper. This stone is used in decoration with cutting and matting capabilities.
glass handicrafts training with free blowing method
From its introduction in the mid-1st century BC until the late 19th century, this method had a prominent place in the teaching of glassmaking and glass-shaping, and is still used today as a glassmaking technique, especially for artistic purposes. The free blowing process involves blowing air into the molten glass at one end of the tube. This happens due to the creation of an elastic skin inside the glass bubble. After this process, the glazier can quickly blow the molten glass and make it into a consistent and desired spot.
glass handicrafts materials
1. Basic elements in glassmaking: Silica or silicon oxide is the main ingredient of all glass products, which exists in the form of sand, flint or porcelain stone. Boric oxide is used as the main element in making glass.
2. Melting elements: These elements, such as soda in the form of sodium carbonate, sodium sulfate, sodium acetate, lower the melting point of silica and give the glass an alkaline state.
3. Stabilizing elements: These materials are used for better mixing of the main and melting materials and also to prevent the glass from dissolving in different materials. Calcium carbonate is one of the most common stabilizers.
4. Bleaching elements: they use another color to neutralize one color in the glass paste; For example, they use green to neutralize red.
The tools used in the traditional glass workshop:
1. Bori (tail rod): This tool is a hollow steel tube with a length of 120 to 150 cm and a diameter of 1.5 to 2 cm. which is used to remove molten glass from inside the furnace.
2. Work stone: stone or metal is used to heat the materials on the tail rod.
3. Wooden spoon: in the form of a mortar that is always wet and has the role of a mold.
4. Water device: a rectangular cube metal basin that contains water and is used for cooling.
How to glass
1. The first stage
Calmly and slowly dip the end of the tailpipe into the furnace (bar, i.e., a suitable material that is available in the furnace and includes the combination of silica and glass) in the furnace and turn it a little to absorb a little load. to be
2. The second stage
In this part, take the tail out of the furnace in such a way that you rotate the tail around its axis, rotate the tail in different directions so that the load does not “wind” as it is known and is stable in the head part of the tail.
3. The third stage
In this part, knead the load that was fixed in the cold stage on a smooth piece of iron (stonework) and finally, the final part of the load is connected to the simplified surface so that it cools down a bit. This work is also called stone work.
4. The fourth stage
In this part, we have to die in our material so that a bubble with a diameter of 5 to 7 cm is formed. In the last part of making the initial bubble, you wait a few minutes until the ball cools down and its color returns from red to the desired color.
5. The fifth stage
In this part, we have to take the initial ball inside the furnace and heat it and rotate the ball again so that the load sticks to it.
6. The sixth stage
After the tail pipe is removed from the furnace again, but this time we have to rotate the pipe on its axis, but this time we do not limit ourselves to this and rotate the pipe in other directions as well.
7. The seventh stage
We blow again inside our bubble to make it bigger and then we put it inside the wet spoon and turn it around; With this, the bubble becomes colder and becomes pasty, and the blowing process becomes easier in the next parts, and finally, it makes the glass uniform regardless of the thickness throughout the entire work.
8. The eighth stage
In this part, depending on how long the neck of our container is, we must bring the pliers closer to the throat and as we are rotating the container around its axis, we bring the pliers closer to the end of the bubble with a little pressure.
9. The ninth stage
In this part, you have to put enough pressure in the throat of the bubble and the tail so that the diameter of these two parts becomes the same and a groove is created in that part.
10. The tenth stage
At this stage, the final brew is given inside the bubble, which depends on the size of your container; That is, you have to blow the same amount into the glass and smooth the bottom of the glass at the same time to achieve the required balance.
11. The eleventh step
In this section, one person should come to the help of the master worker to put a little pressure on the center of the flat part of the work with a pipe called a pipe so that a dimple is created; This work maintains the balance of the work in the principles of glassmaking.
12. The twelfth step
At this stage, the master makes a scratch with a knife on the groove created in the ninth part and then pours a few drops of cold water on it and does all this while rotating the dish.
13. The thirteenth step
Here we have to separate the container from the clamp, first we pour a few drops of cold water in the desired place, then we separate it with a slow blow and put the jar in the oven to heat up a little and soften.
15. The fourteenth stage
When the water in the container is hot, we should press it slowly until the diameter of the container opening reaches the required size.
16. The fifteenth stage
In the last step, the container is transferred to the hot house to remove the contagion from it, now we have to leave the container alone for 48 hours so that it stays in the hot house and cools down, and at this time the temperature of the desired place is 500 degrees. Satnigrad slowly decreases to 20 degrees Celsius.
Modern glass making training
The conversion of raw materials to glass is done at about 2400°F (1320°C). At this point, the glass emits so much heat that it appears almost white and hot. After this, the glass is left to bubble out of the mass of raw material, and then the working temperature in the furnace is reduced to about 2000 degrees Fahrenheit (1090 degrees Celsius). At this point, the glass will appear bright orange. However, most of the vitrification process is done between 1600 and 1900 degrees Fahrenheit (870 and 1040 degrees Celsius). Sodalim glass, for example, remains somewhat plastic and can work up to 1,350 degrees Fahrenheit (730 degrees Celsius). Annealing is usually done between 700 and 900 degrees Fahrenheit (371 and 482 degrees Celsius).
glass handicrafts training at home
You need a few basic tools to make glass at home; The first is glass rods, which can be found in different sizes and colors. The second case is Mandrel; Hot glass is wrapped around mandrels. The third is Marving pages; These items are tools that are used in the finishing stages of glass making. They are usually made of metal and help smooth out your work. The glass is rolled over the surface of the cavity while it is cooling to get rid of any lumps or bumps that are not ideal in a final piece.
The fourth item is the work lamp burner; Instead of a large grill, you need a small burner and a fuel source such as a propane tank. A high-quality torch is the most important tool for home glassmaking. The fifth necessary tool is Bead Release; This is a liquid substance that mandrels are dipped in to prevent glass shards from sticking to them. Using this device allows you to use the mandrel over and over again. The sixth item is a rake and a small hammer; The rake in glassmaking is a small metal rod with a curved end, and the hammer has a strong, protruding head. These two tools shape the hot glass and allow you to twist, stretch and compress the glass as needed.
The seventh item is a cooling fiber blanket (instead of an annealer); Fiber blankets are used for cooling. Most of them can withstand heat up to 2300 degrees Fahrenheit. Finally, we have the most important part of home glassmaking training, which is safety equipment; Safety equipment such as gloves, goggles and aprons are essential. No glassmaking course is worth learning without these safety tools in mind.